“Environmental control systems tend to be treated rather like the Cinderella of architecture; given only the plainest clothes to wear, they are relegated to a back room to do the drudgery that maintains the elegant lifestyle of the other sisters: light, form, structure, and so forth."
~ Lisa Heschong [1]
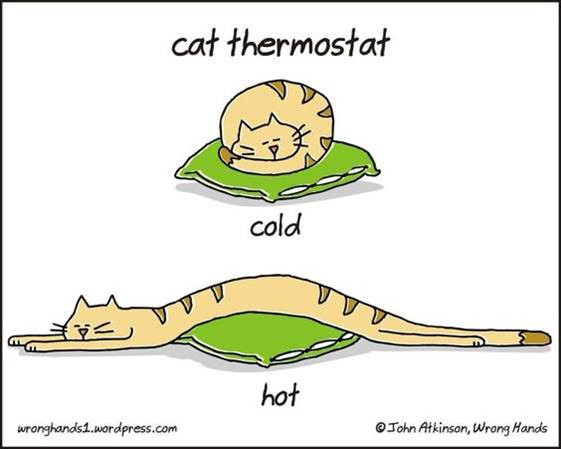
Early in 20th century, architecture was profoundly impacted by the industrial revolution and increasing availability of machinery to mechanically control the internal temperature and humidity of buildings. Architects were liberated by their new freedom to design with little or no regard for thermal comfort. Architects all but abdicated that responsibility, delegating it to consulting engineers. This remains the status quo to this day, as many architects think about 'HVAC' (Heating, Ventilation, Air Conditioning) systems as an afterthought at best.
Architects inspired by the German Passive House technology are changing that. We design with a holistic interest in more intelligent, resourceful, and responsible architecture. As we reclaim these capabilities our practices have, of necessity, become inclusive of advanced building science and sophisticated technologies.
Architects, engineers, contractors and manufacturers tend to use different terminology, jargon, and acronyms when talking about climate control systems, and the data used to classify and describe them. In the passive house universe, where we build well above mainstream convention or codes, we often encounter contractors who are challenged to understand the dramatically different scale of the systems required, the very low loads, and the unique challenges of conditioned air distribution. Moreover, this is not simply a matter of scaling down a larger system or using a small-house system in a larger building with an equivalent load.
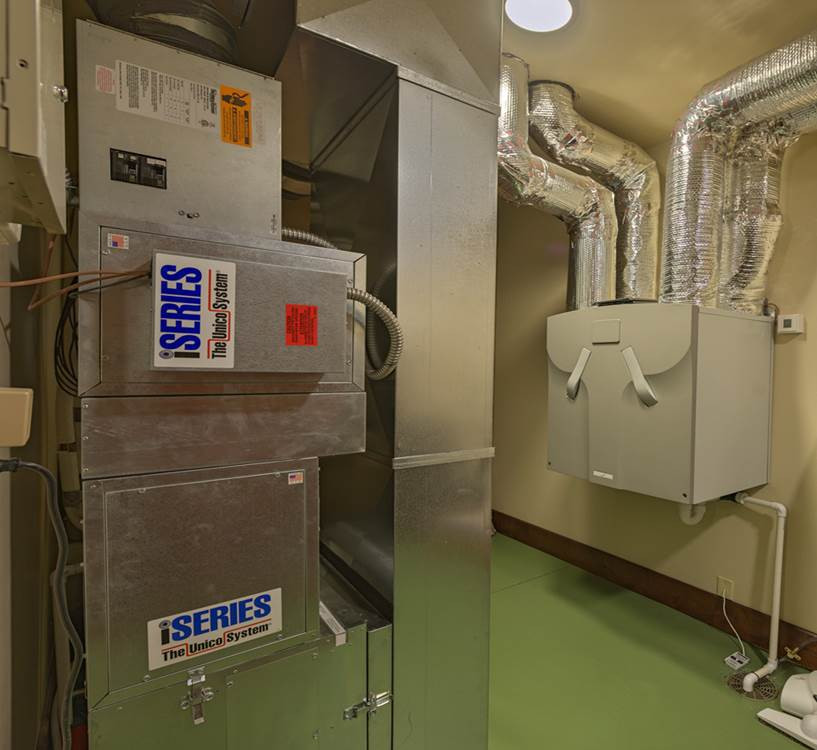
Most of our clients don't care deeply about their comfort systems - as long as they consistently work well. So not only do we treat HVAC systems like Cinderella, but we also treat them like so many other things in life taken for granted. We only notice them when they fail, or when the diffusers are ugly, noisy, or drafty, or when a duct or return plenum interrupts a perfect wall or ceiling plane. But regardless, a well designed and properly installed mechanical system is a thing of beauty. The quality of construction of an entire project is usually made apparent by the care taken in the mechanical room.
Certified Passive House architects have a deep understanding of building science and heat flow calculations, and tend to obsess over technical topics such as R-values, thermal bridges, and window spacer psi-values. We cannot be satisfied with the 'old-school' rule-of-thumb methods and one-size-fits-all answers that persist in the construction industry at large. Our office uses an extremely powerful tool software tool from Germany we refer to as WUFI (Wärme - Und Feuchtetransport Instationär, or 'thermal and moisture analysis') that gives us a tremendous amount of information about the thermal performance of the building we are designing and serves as our main data conduit in our interactions with the Passive House Institute US (PHIUS), as WUFI models are the preferred metric for project certification with PHIUS.
We begin by understanding our client’s specific expectations of comfort. How many days of the year, if any, are they happy to put on a sweater instead of turning up the heat? Will they go barefoot year-round, and do they favor carpet, hardwood, or concrete floors? In a passive house with a well-insulated floor, the surface temperature might be acceptable on a concrete floor, but because our skin temperature sensors measure delta, not absolute, we sense that concrete floor as colder than a wood floor at exactly the same temperature. Do we want cooling in the summer, even if it might be needed for just a few days or weeks? Is this a home for retirees, who might be more sensitive to temperature fluctuations? Does one family member prefer 68 degrees while another expects 76? It is possible to meet or exceed most expectations if care is taken in design.
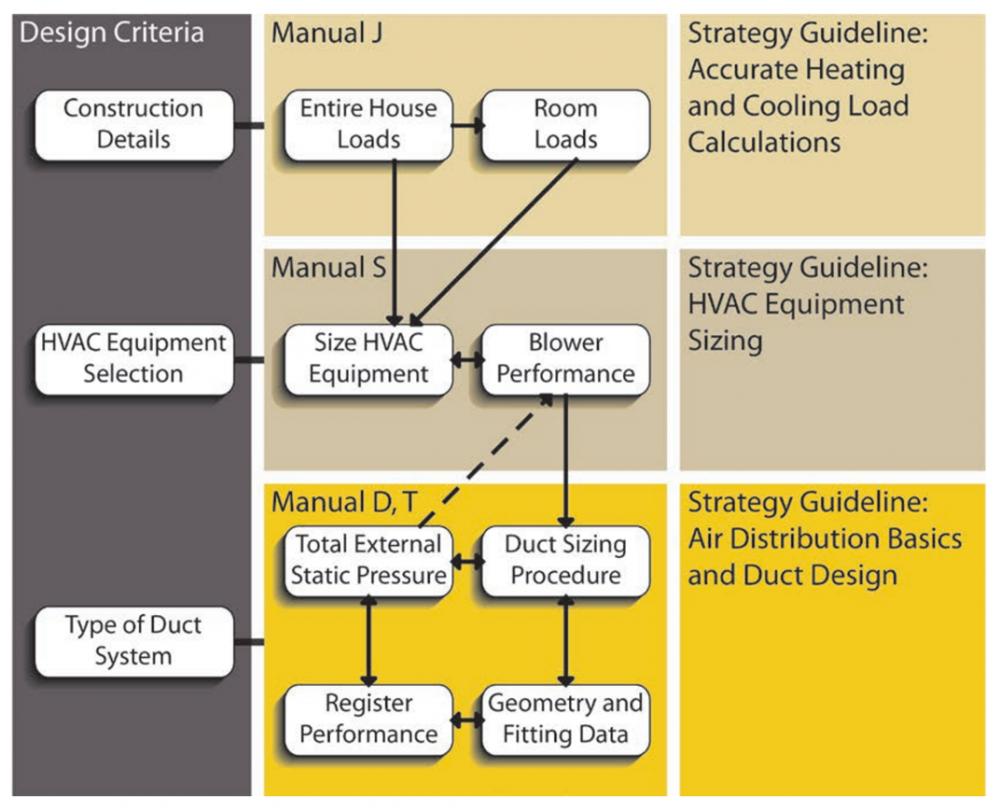
ACCA (Air Conditioning Contractors of America) has developed the protocol and standards for calculating heating and cooling loads adopted by ANSI (American National Standards Institute), ASHRAE (American Society of Heating, Refrigeration, and Air Conditioning Engineers), and many building codes. These are the tools most broadly used by HVAC contractors and engineers. 'Manual J' estimates residential heating and cooling loads; 'Manual N' is similar but for commercial buildings. 'Manual S' is for sizing equipment, because there is a big difference between load and capacity. 'Manual T' calculates air distribution, and 'Manual D' is for sizing the Duct system and layout.
Like WUFI, Manual J also gives us a peak heat load and cooling load, but uses slightly different methods and parameters. There is often a substantial difference between WUFI Passive loads and Manual J. There are a few big reasons, and many small ones.
This conversation starts with load calculations, or calculating the magnitude of heat moving into and out of a building and the amount of thermal energy that will need to be supplied by mechanical heating and cooling. Design loads are usually given in British Thermal Units per Hour, or BTUH. 12,000 BTUH, or 12 kBTUH equals 1 'ton' of heating or cooling. Equipment sizes are often described in ton ratings, but in the world of passive house we tend to stick with BTU. Calculating loads generally starts with a building enclosure, initial conditions, then considers heat loss (or gain) by transmission, infiltration/ventilation, internal loads (appliances and people), and solar gains.
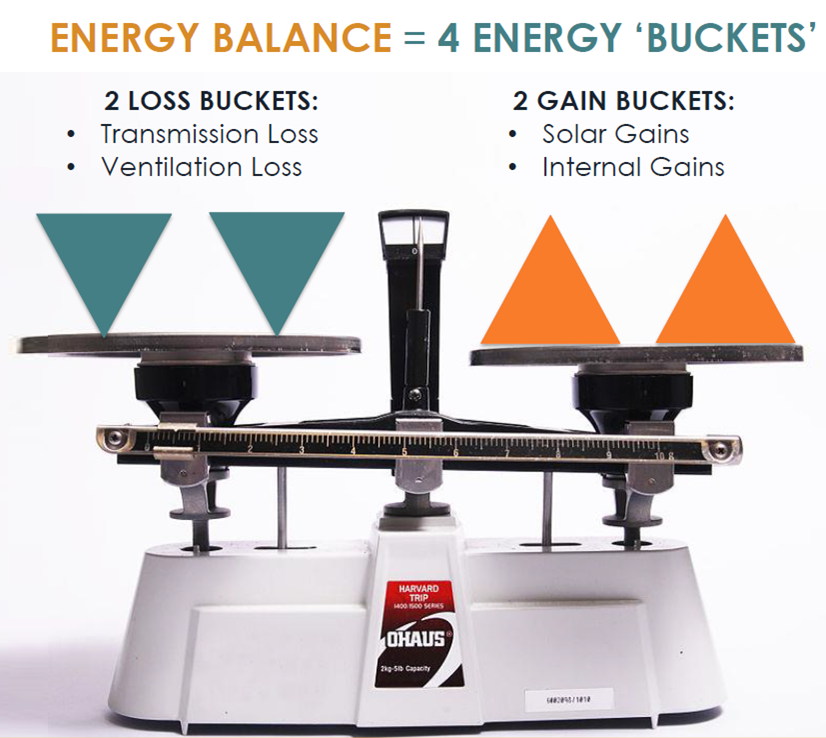
Peak loads are the amount of thermal energy required to maintain a desired level of comfort at the worst case heating or cooling condition. The equation for calculating the peak heat load is: Ph = Pt + Pv – (Ps + Pi) Heat transmission (Pt) and Ventilation (Pv) are offset by Solar (Ps) and Internal Gains (Pi). We design mechanical equipment systems to cover the difference, and that difference is the Peak Heat Load. (Or Peak Cooling Load in the summer.)
The difference between WUFI Passive and Manual J with the biggest impact on Heat Loads is the approach to solar gains. Manual J doesn’t give credit in the heating season for internal gains or solar gains. Both are seen as a penalty in the cooling season, of course, but not as a benefit in the heating season. The assumption is that the peak condition or peak heat loss occurs at night and during periods of occupant inactivity, so the Manual J winter design condition is an empty house, no people or appliances, or windows - other than the low R-value dark hole in the envelope - no windows in winter. WUFI Passive does give credit for the occupants and appliances that might be providing incidental heat, even in the coldest hour of the coldest night in the deepest winter as well as the thermal storage, or thermal lag, we’ve designed into the building - the ability for the thermal mass to help the building ride through the extremes. If we set all the windows in a WUFI model to full shade and take out internal gains, the heating load resembles Manual J results.
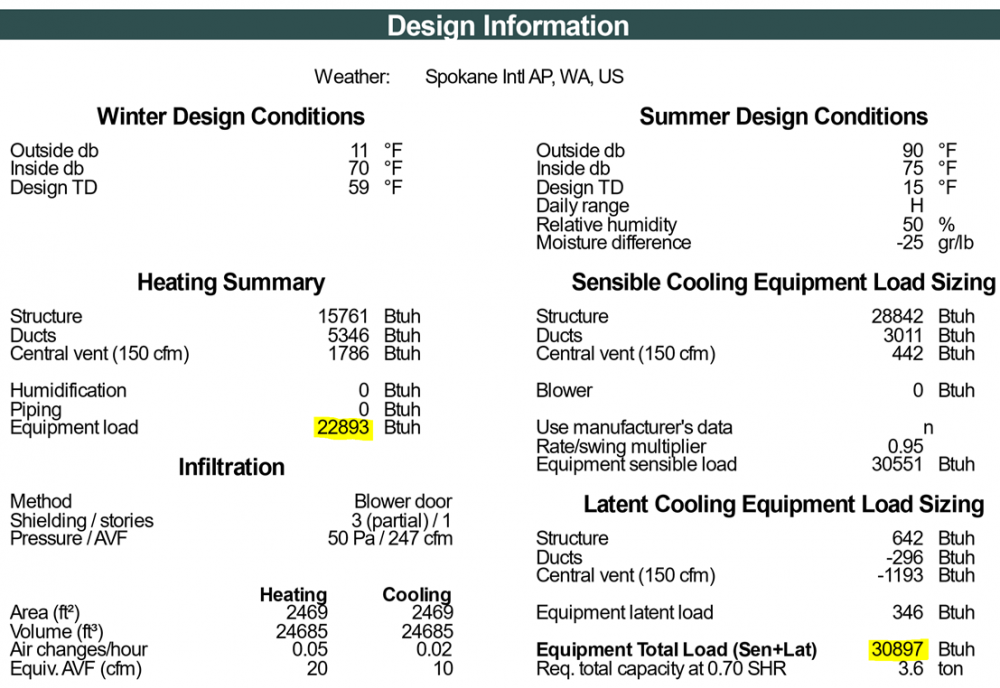
The next big difference is in design temperatures. The default Manual J indoor temperature setpoints are 70F and 75F, where PHIUS (Passive House Institute US) protocol sets those at 68F and 77F. A super-insulated structure responds more slowly to changing outdoor conditions, so peak loads are moderated. Because the temperature of indoor surfaces is less extreme, less radiant cooling allows wider swings in ambient air temperature without affecting comfort level. Manual J is set up for use with a much broader range of building performance, from way below code to passive house standard, so assumes a more conservative approach to indoor comfort levels. PHIUS recommends against taking the WUFI Passive design temperatures and using them in a Manual J calculation, but rather, run each method on its own terms and compare the bottom line Btu/h results.
There are a few different options for choosing outdoor design temps, and it’s such a basic parameter that it is easily overlooked. ASHRAE recommends using the 99% and 1% dry bulb temps, or the temperature your climate stays above for 99% of the hours of the year (or below for 1%) so a system is considered big enough if the capacity exceeds the load for all but 88 hours of the year. ASHRAE 99.6% is also used in some cases. WUFI Passive takes from the climate data the average daily mean temperature from the two worst-case winter days: cold and clear with more solar gain, or cloudy and not so cold. Summer design temperature is the highest daily mean. These usually end up less severe than ASHRAE so the predicted difference between the interior and exterior climate ('delta T' in engineer-speak) is lower from both the indoor and outdoor side. Either way, the goal is to size the equipment to cover “almost” all of the worst possible hours of a typical year.
The formula for heat loss is Q = UA ΔT. That delta T is multiplied out by the area and thermal conductivity of every exposed surface, so can make quite a difference in the total peak load. The magnitude of this difference merits a discussion with not only the HVAC designer but also the client on how to prioritize comfort and economy, and right-sizing the equipment.
Calculating shading is a complicated process, and WUFI Passive and Manual J take different approaches. Manual J window parameters include a Yes or No option for exterior shade, five options for internal shades with a percent closed entry, insect screen coverage, and overhangs. The current version of WUFI can now calculate true geometric shading elements like trees and neighboring buildings in the visualized geometry, with a mean monthly shading factor based on the sun angle. Shading from building geometry is calculated as well as window reveals, which in a passive house with thick walls and windows semi-recessed into deep walls can be significant.
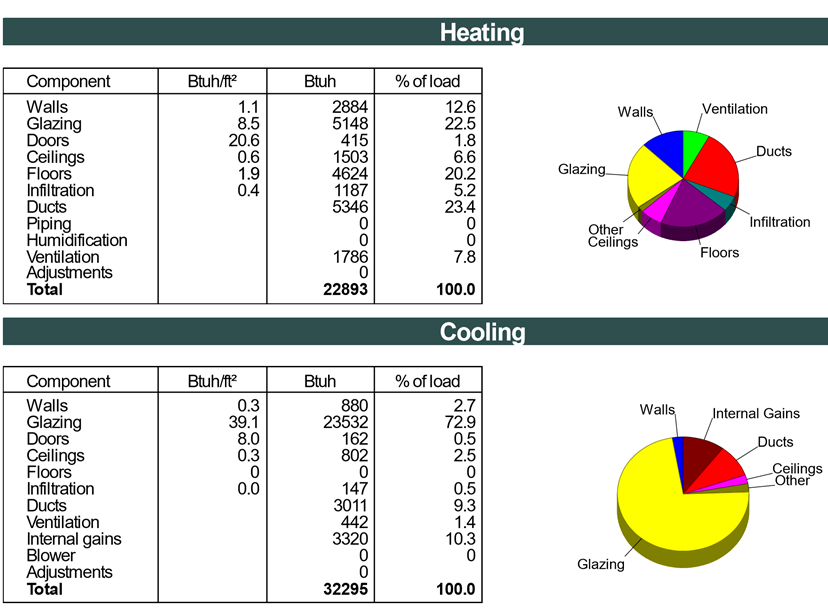
The pie charts show the load breakdown in a Manual J Report. You can compare this to the breakdown in a WUFI Passive report, by enclosure surface, glazing, ventilation and infiltration, and gains. Comparing categories can give more insight into reconciling the two analysis methods.
High-performance homes are getting more and more airtight and are so far above the norm that it makes a significant difference in equipment sizing. In WUFI we can enter the exact result of a blower door test. Some Manual J software platforms now have this capability, but standard practice is still the simplified method, choosing from the five ASHRAE categories of airtightness - Tight, Semi-tight, Average, Semi-loose, and Loose. The highest category, or Tight, roughly corresponds to the old PHIUS infiltration target of 0.6 ACH50 (Air Changes per Hour under 50 Pascals of pressure). But the new PHIUS standard of 0.05 cfm/sf of envelope only matches up in buildings of about 1500 - 2000 sf iCFA. Larger projects will tend to be much tighter than the ASHRAE standard, and smaller projects will be less tight so the infiltration loss might actually be understated.
Manual J can give a detailed room-by-room or zone calculation. WUFI can too, but only once you get deep into the dynamic side and set up zones. Another reason Manual J often shows higher cooling loads is the calculation for exposure diversity, or the tendency for a room with all west-facing glass, for example, to need more cooling in the evening than a room with greater diversity in the orientation of the glazing.
Anyone who has experience running a WUFI model or has used Manual J will understand how many hundreds of data points are included in what seems to be a simple, four-part equation, and each of these data points leaves room for a difference in results. The method for defining assemblies, with the framing factor listed as a percentage rather than dimensions in section, options for selecting climate conditions and design temperatures, defaults for appliances and energy use, number of and loads attributed to occupants, thermal lag, and too many more factors to list lead to small differences that can compound into large changes in calculation results.
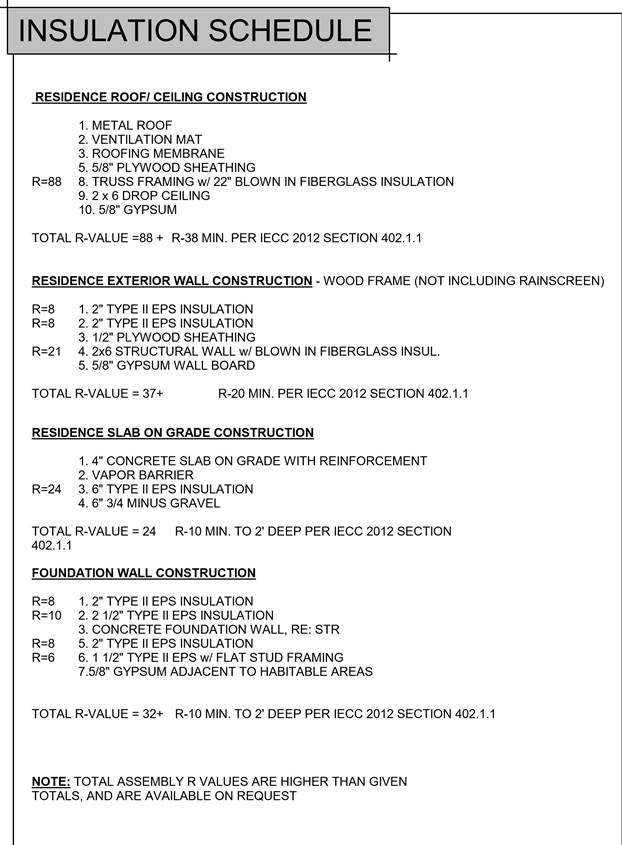
While there are many differences between Manual J and WUFI Passive, both are valuable tools. The best path to success in HVAC design is good communication with the entire project team. The Manual J calculations will be much more accurate if there is a systematic and complete communication of project data between the architect and engineer. We’ve developed office standards to share information from the WUFI model with the builder, HVAC designer, and relevant subcontractors. Standard legends in our construction documents list specific assemblies and R-values, window performance data, loads and ventilation requirements. We also specify shading and interior blinds here along with all the other important information that will impact design loads.
The four categories of heating and cooling components of any type of comfort system are: source, distribution, delivery, and control. Thousands of years ago an open fire (the source) in a pit at the center of a dirt-floor shelter gave radiant heat (distribution) to occupants huddled around the firepit (delivery), adding fuel as they got too cold (control). Now, systems are more complex and varied.
Once loads are properly calculated, specifying proper equipment is important. We favor heat pumps because they are efficient and broadly applicable to passive house projects. They don’t require combustion, and they have much higher efficiency than electric resistance heat. Common terms used to describe heat pump systems include 'mini-split', 'ductless heat pump', or 'split system'.
A ductless mini-split usually refers to a one-to-one pairing of an indoor wall-mounted unit with a matched outdoor compressor, but can also include short-run ducted fan coil units. We still call these split systems ductless heat pumps because the heat generation (actually, in heat pump technology it’s more like heat collection than generation) has been moved outside and the heat is transported to the distribution point via refrigerant. We’ve taken out the ducts between heat generation and heat delivery, then put them back in for short-run distribution.
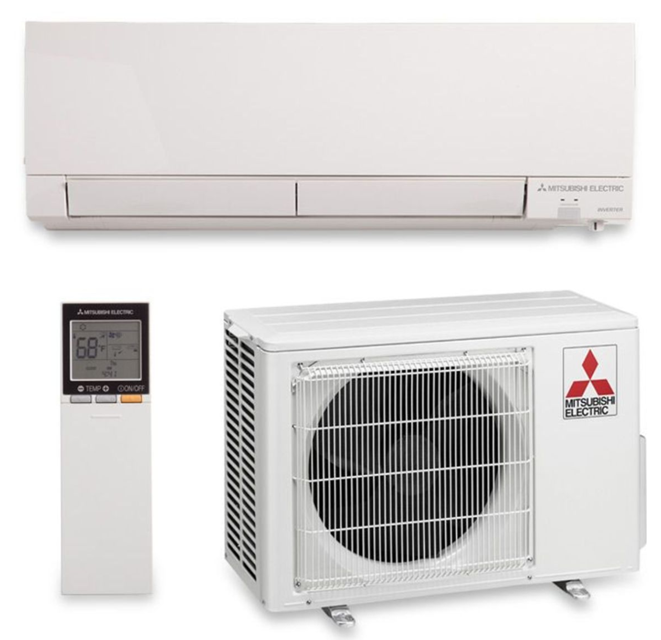
If the highest priority for a project is efficiency and the climate and loads will allow for it, a one-to-one mini-split system with an outdoor compressor and an indoor wall hung unit is a common, economical solution. No ducting and great 'turn down ratios' (the capability to provide small amounts of heat efficiently) yields better performance over a wide range of conditions. Low output options for super-low passive house loads are widely available.
If the budget allows it, we don't need to see mechanical equipment hanging on a wall. A short-run ducted unit hidden above the ceiling has the added advantage of spreading heating or cooling to several rooms in a low-load building. Using one higher capacity internal unit with multiple diffusers rather than one or several single-point wall hung units will perform more effectively and discreetly. This is similar to the comfort system you might see in a higher end hotel room, usually mounted above the ceiling over the entry passage from the corridor. (It is actually not unusual to see equipment made to serve one room like that actually being more than sufficient to condition the interior climate of an entire passive house residence.)
Static pressure of ductwork is a critical consideration in any ducted system, as we may be trying to move more air longer distances than some equipment is designed to handle - which is usually just a few feet away to diffusers in one room rather than multiple rooms where duct runs will be several times longer. The capacity may look sufficient, but if the fan can’t push enough air to the end of those duct runs, the heat won’t get to where it needs to go. Many units do have a higher static pressure (something in the range of 0.6 or 0.8 inches of water column) but might be sent from the factory set at a lower fan speed. If the system is designed with longer runs, the installer needs to check this setting at installation.
There is a big difference between load and capacity. Manual S helps to solve this problem. Product specification sheets describe capacity, but know that the obvious number (nameplate rating) is a rated capacity in ideal conditions at a certain outdoor temperature. This number will change based on climate conditions, equipment pairing, and installation.
Most equipment is tested to the AHRI (Air Conditioning, Heating, and Refrigeration Institute) standard at 47 and 17 degrees F, with an indoor temperature setpoint of 70 degrees. There is a decline in efficiency AND capacity at lower temperatures. If you are designing for a cold climate, you’ll need to know the balance point of the heat pump. As the outdoor temperature goes down, the heating capacity of the heat pump goes down as well, then at some point you’ll reach the temperature at which the capacity equals the load, or the balance point. If the temperature drops lower, the heat pump can’t make enough heat to meet the load. Also, some units shut off completely at around 15 degrees F, some at 5, -7 or even -13. If either of these conditions create a situation where the heat pump can’t meet the load, then you’ll need supplemental electric resistance heat. In cold winter climates, parts of Zone 5, and certainly Zone 6 and above, choose outdoor units with HyperHeat or similar technology to not only increase efficiency at lower temperatures, but also to extend the extreme lower range of operational temperature. Marine zone 4 and 5 might not need to worry so much. Until this year! I’ve been talking to some of our PHIUS people in Chicago about the recent polar vortex and have anecdotal evidence of heat pumps operating at -27 degrees! So, search through submittals and data sheets to find a tested capacity as close to your design temp as possible to see if the unit will provide enough heat when it is most needed.
The Northeast Energy Efficiency Partnership (NEEP) has published a list of air source heat pumps recommended for cold climates. The lists includes rated data for over a thousand units, most with performance specs - capacity and COP - down to 5 degrees, and some to -13 degrees or lower.
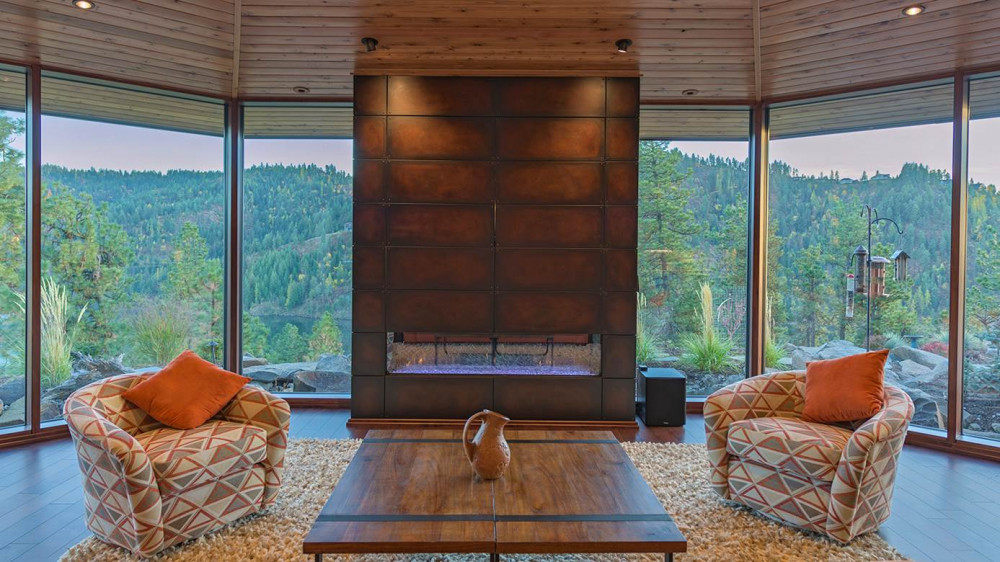
A passive house can present unique challenges in zoning and distribution. A small, well-designed passive house with a compact building form and very low loads probably won’t need zone control. But a passive house with optimized orientation for solar gain might have south-facing rooms that need much less heat during a sunny winter day compared to north-facing rooms, but because of increased glass area might need more heat at night. Good zone control can help solve this imbalance. Multi-story projects may need to address naturally occurring stratification internally as heat rises to upper levels. Clients may prefer to have bedrooms cooler for sleeping or exercise. It all comes down to specific client preferences and the overall design context.
That brings us to the last of the four elements: controls. Current technology is bringing more options for fixed and remote status monitoring and control. The installer and manufacturer should confirm these systems can talk to each other and won’t interfere with the normal feedback loop of the mechanical equipment. With the big steps forward taken by passive house champions in providing thermal comfort, proper humidity, and clean fresh air, there is a big opportunity to also improve monitoring and control.
Air Conditioning Contractors of America: www.acca.org
Building Science Corporation: www.buildingscience.com
Green Building Advisor: www.greenbuildingadvisor.com
PHIUS+ Certification Guidebook: http://www.phius.org/PHIUSPlus2015docs/PHIUS+%20Certification%20Guidebook%20v1.1.pdf
Mechanical and Electrical Equipment for Buildings by Walter T. Grondzik and Alison G. Kwok
[1] Heschong, Lisa, Thermal Delight in Architecture MIT Press 1979